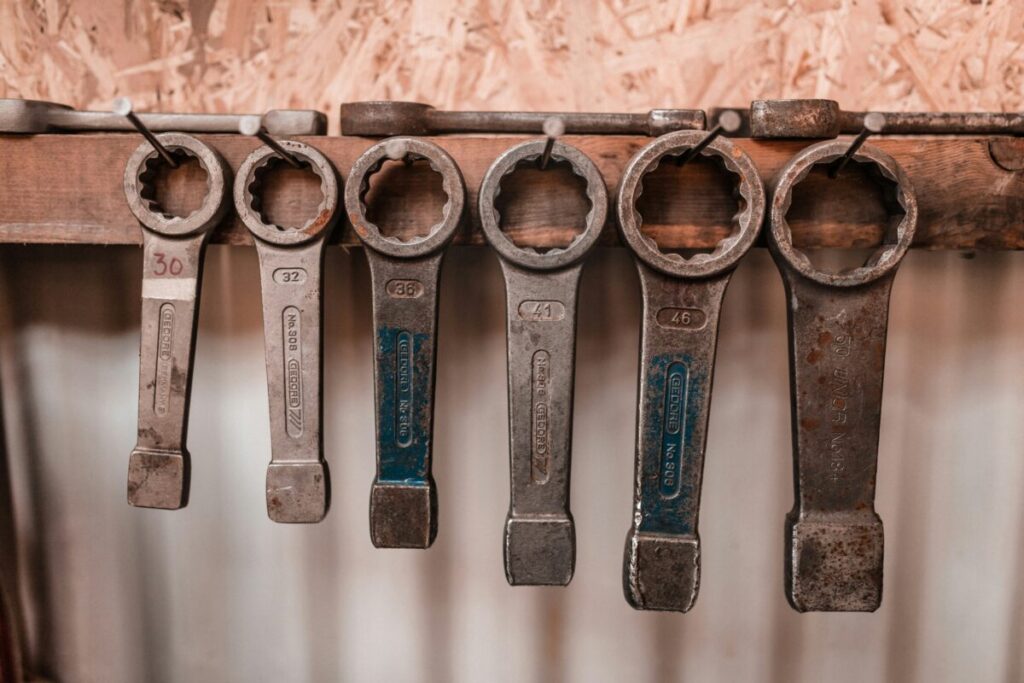
QCとはQuality Controlの略で、日本語では品質管理のことです。製造業を中心に非常に大切な考えです。
「パレート図/特性要因図/グラフ/ヒストグラム/散布図/管理図/チェックシート」は7つ道具と呼ばれます。
今回は「どの対策が一番大切かが一目でわかる」特徴を持った「パレート図」を簡単に説明してみます。
課題:出荷するおもちゃの故障が多い
原因 | 件数 |
内部の断線 | 50件 |
表面の割れ | 30件 |
組付け不良 | 20件 |
あなたはとあるおもちゃ工場の製造担当者ですが、担当しているおもちゃに故障が多くて困っています。
対策を行うためたくさん壊れる原因から順番に整理すると、大きな原因が3つあることが分かりました。
故障した原因を全部足すと100%になることから、わかりやすいように故障品を100個取り出して数えます。
- 内部の断線(おもちゃ内の銅線が切れる)→ 50個
- 表面の割れ(プラスチックが割れる)→ 30個
- 組付け不良(ネジがゆるいとかで壊れる)→ 20個
棒グラフ:原因が占める割合
原因 | 件数 | 故障に対する割合 |
内部の断線 | 50件 | 50% |
表面の割れ | 30件 | 30% |
組付け不良 | 20件 | 20% |
今回は故障品を100個取り出して調べたので、原因の個数と原因が故障品に占める割合は等しくなります。
「内部の断線:50%、表面の割れ:30%、組付け不良:20%」です。(割合=原因数÷故障品の合計数)
それでは一度Excelでわかったデータをまとめておきましょう。横軸が原因、縦軸がそれぞれの割合です。
全部足したら100%になるよね?
原因 | 件数 | 割合 | 累積割合 |
内部の断線 | 50件 | 50% | 50% |
表面の割れ | 30件 | 30% | 80% |
組付け不良 | 20件 | 20% | 100% |
今回は故障品すべてを3つの故障のどれかと結論付けたので、全部の割合を足せば100%になるはずです。
では試しに割合の大きい原因から順番に足し算をしてみましょう(大きいほうからする理由は後ほど)
50%(断線)、50%+30%=80%(断線+割れ)、50%+30%+20%=100%(断線+割れ+組付け不良)です。
それではここでもExcelにわかったデータをまとめておきましょう。先ほどの表の隣に「累積割合」を。
累積とは、数値を1つずつ順に足し合わせていった合計のことを指しことで得られる値です。
折れ線グラフ:対策による効果の大きさ
故障品がそれぞれどのような原因で故障するかがわかりました、では次にどこから対策していきましょう?
割合の大きいものから対策すれば故障品を減らしやすいのはわかりますが、最終的なゴールはどこでしょう?
例えば今回の目標が故障品を現在から8割減らしたいのであれば、80%分の対策をすればよいことになります。
パレート図の嬉しい所
「おもちゃがどの原因で一番壊れてるか」だけを知りたければ、割合を示した棒グラフだけで分かります。
しかし「いくつかの原因の合計が全体の中でどれくらいの割合を占めているか」は一目ではわかりません。
パレート図を用いることで累積割合や、「どこまで直せば大きく改善できるか」がすぐに分かってきます。
一般に対策を行うときは目標を定めて、それに対して最も効果的な方法を使おうと考えるのが正攻法です。
パレート図のExcelでの作り方
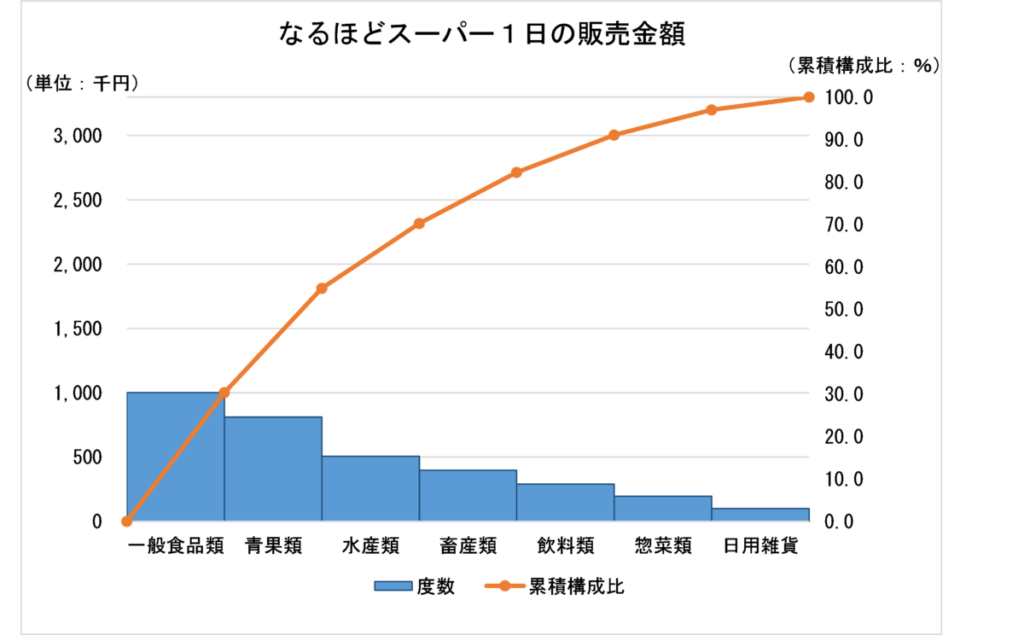
実際の作り方を紹介しようと思いましたが、こちらのサイトでばっちり説明されていましたので割愛。
こちらの「なるほど統計学園」は総務省統計局が提供しているサイトで、非常にわかりやすかったです。